Introduction
Crimped terminations are a widely used method of connecting wires to various devices as well as for creating so-called splices - that is, wire-to-wire connections.
There are open barrel terminals, closed barrel terminals, machined contacts, and ferrules.
A properly executed crimped termination is crucial for the reliability of the entire system. As is well known, a single improperly made crimp can lead to failure under stress factors such as vibration, constant mechanical pressure, temperature effects, or current flow. Therefore, understanding the requirements for such connections is extremely important.
This article presents the requirements for crimped terminations, using the open barrel terminal as an example. These requirements are based on the IPC/WHMA-A-620 standard, one of the key documents about manufacturing cables and wire harnesses.
Enjoy the read! :)
General Requirements
The following general rules are among the most important to consider when making any crimped termination:
- Only stranded wire. Crimped terminations should only use stranded wire. Solid wire is not allowed. Crimping relies on the compression of multiple strands, which cannot be achieved with a single solid conductor.
- No tinning of strands. Crimp terminations shall be made using stripped strands (copper or plated). Do not tin (solder) the strands prior to crimping, as solder may crack and/or will be displaced under pressure, leading to a loose connection.
- No strand trimming. The cross-section of the conductor shall not be reduced to fit the terminal. If the terminal is too small or not suitable - a different terminal or conductor should be selected.
- No twisting of strands. Conductor strands should be inserted into the terminal without deformation or twisting. Twisting alters the shape and size of the cross-section and increases the risk of damage or strand cutting during crimping. Unfortunately, this mistake is common (often seen in practice and in YouTube videos) but is a serious error.
- Combining wires is allowed. Multiple conductors may be crimped together in a single terminal. However, the combined cross-section shall match the terminal size, and strands shall be inserted parallel to each other. Do not twist strands together to form a "single" conductor.
- Do not re-crimp terminations. Once a crimp has been made, it shall not be re-crimped. Re-crimping introduces excessive mechanical stress to the terminal material, weakening it and increasing the risk of cracking.
- Use the correct tools (applicator). Achieving a proper crimp, and therefore the required reliability, largely depends on the tools used. Be cautious with inexpensive "universal" hand tools - they often cannot ensure IPC-compliant crimps. Professional-grade tools matched to the terminal type can be pretty expensive (in the case of hand crimpers, often several thousand PLN), which is why hobbyists rarely use them. However, in professional applications where high reliability is required, using high-quality tools is essential. Cutting costs on tools often results in greater losses than investing in the right equipment.
Example Defects
The illustrations below show selected examples of defects considered as defects for all three IPC product classes. The crimped termination type shown is the open barrel terminal:
1. The insulation end is not visible in the insulation inspection window:

2. Insulation intrudes into the conductor crimp zone:

3. No bellmouth at the conductor entry point:

4. Wire strands are not visible exiting the conductor crimp zone:

5. Strands extend into the contact area of the terminal:
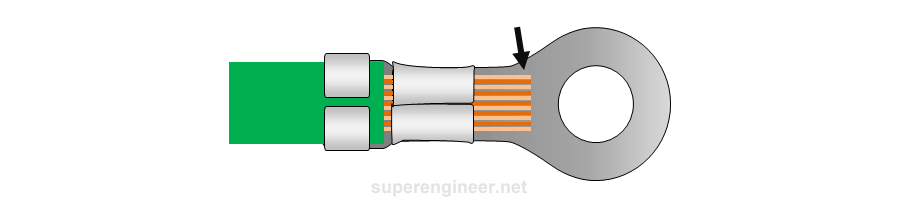
Inspection Methods
The following methods are used to inspect product characteristics in crimped terminations:
- Visual inspection. The IPC/WHMA-A-620 standard defines acceptance criteria in Chapter 5 and specifies the required magnification for inspecting crimped terminations in Chapter 1. For example, for wire diameters greater than 1.63 mm (14 AWG), inspection can be performed with the naked eye. For diameters between 1.63 mm and 0.64 mm (14-22 AWG), a magnification of 1.5x to 3x is required. More details are provided in Table 1-1. Adequate lighting is also required (minimum 1000 lux).
- Crimp height measurement. Crimp height depends on the type of terminal and the cross-section of the conductor. Verifying that the crimp height falls within the specified range is described in Chapter 19 of the IPC/WHMA-A-620 standard.
- Pull force testing. Crimped terminations shall be tested for tensile strength. The criteria for this test may be specified by the design (customer), terminal manufacturer, or based on standards such as SAE, UL, or Chapter 19 of IPC/WHMA-A-620.
It is recommended that crimp height and pull force testing be covered under statistical process control (SPC). This approach enables continuous monitoring and improvement of the crimping process. Naturally, the process should undergo risk analysis using P-FMEA, and the resulting control methods should be included in the control plan. The measurement system used shall also be capable, which should be confirmed through a Measurement System Analysis - MSA.
Summary
Creating reliable crimped terminations in compliance with IPC/WHMA-A-620 requires not only knowledge of visual inspection criteria for finished terminations but also the use of proper equipment and the implementation of robust process control.
As we can see, it is very important to understand IPC/WHMA-A-620 requirements and merge them with quality tools and methods like FMEA, Control Plan, SPC, and MSA. That mixture should be a great solution for manufacturing high-quality, reliable wire harnesses, even for the most demanding applications.
Footnotes
- "IPC/WHMA-A-620: Requirements and Acceptance for Cable and Wire Harness Assemblies," Rev. E, IPC International Inc. USA, 2022.