Introduction
SMT reflow soldering is a process in which SMD component packages are heated to temperatures above 200°C. If such an package contains a significant amount of moisture, heating it can cause a rapid release of moisture vapor. The pressure builds up inside the package and leads to swelling, cracking or delamination. Sometimes the level of damage can be so severe that the component fails almost immediately due to the breaking of internal electrical connections (such as bonding).
During the rapid expansion of moisture, when the package is ruptured and steam escapes from it, you can hear a sound like roasted corn turning into popcorn, which is why the effect is called the "popcorn effect" or "popcorning". Sometimes the chip can be so saturated with moisture that it even "pops" during soldering, when steam violently escapes from the chip's package.
The reflow soldering profile and wave soldering profile have a defined parameter, which is the "maximum temperature gradient" to limit thermal stress on components. However, it is important to note that moist components can be damaged despite maintaining the correct temperature profile and soldering time.
So we can conclude that SMD components shall not contain excessive moisture during the soldering process.
MSL level
The IPC and JEDEC organizations have developed the IPC/JEDEC J-STD-033 standard, which addresses the handling (packaging, storage, drying, etc.) of moisture-sensitive SMD components according to the Moisture Sensitivity Level (MSL).
The MSL level itself is formally defined in the J-STD-020 standard "Moisture/Reflow Sensitivity Classification for Non-hermetic Surface Mount Devices (SMDs)."
It is worth noting that J-STD-033 applies to reflow soldering components. It does not apply to other bulk soldering methods (e.g., wave soldering, selective soldering), in which the component package is not heated to such high temperatures as in reflow soldering.
The J-STD-020 standard specifies the following MSL levels:[2].
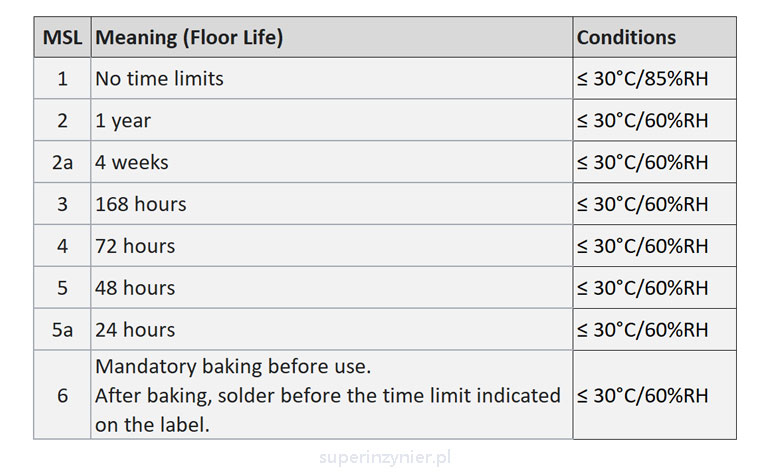
The MSL level specified by the manufacturer is indicated on the bag or label. The following example shows the label for MSL level=3:
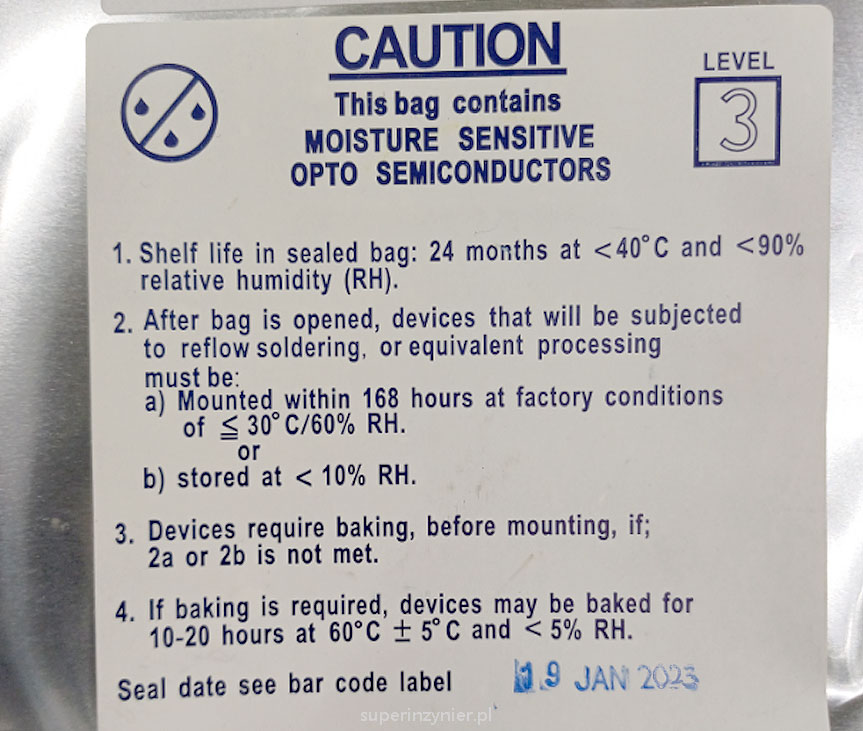
J-STD-033 requires the bag to include a symbol to inform users that its content is moisture sensitive. The name of this symbol is MSID (Moisture Sensitive Identification). See an example image below:
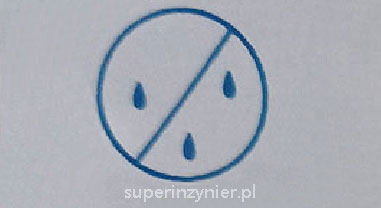
HIC - Humidity Indicator Card
Components with MSL level from 2 to 5a shall be packaged into a bag along with a HIC (Humidity Indicator Card).
The HIC is a card with percentage boxes that contain a chemical that changes color depending on the moisture level. It allows to read the relative humidity level.
Until recently, mainly cobalt chloride solution (CoCl2) of various concentrations was used, which is highly hygroscopic and turns from blue to violet and then to dark pink. Cobalt-free indicators are now available.
The indicator shall:[1]
- Have a minimum of 3 spots for moisture levels: 5%RH, 10%RH, 60%RH.
- Have color change guidelines written on the indicator.
- At 60% relative humidity and 30°C, the 5%RH spot shall change color from 4 to 7 minutes
- At 60% relative humidity and 30°C, the 10%RH spot shall change color within 6 to 10 minutes.
Examples of HIC cards
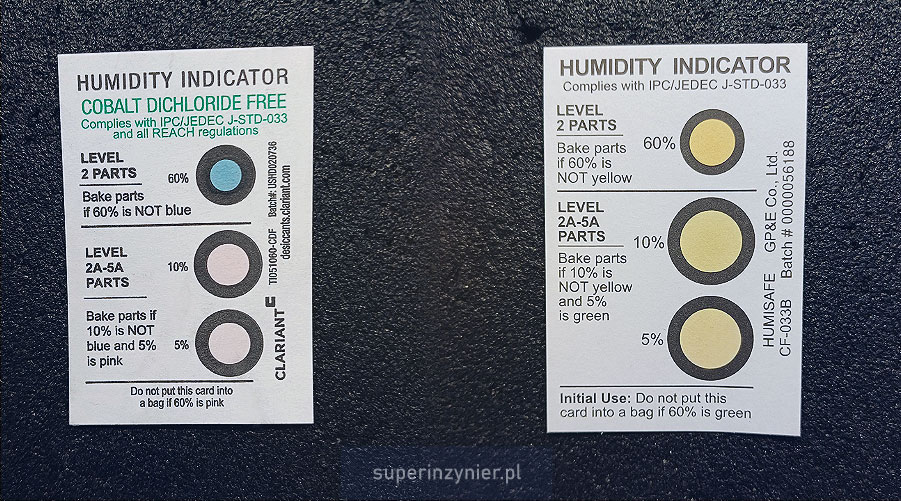
There are 6-point indicators also available. Such indicators have typically following spots: 10%RH, 20%RH, 30%RH, 40%RH, 50%RH, 60%RH. These indicators are used in PCB packaging.
Two types of HICs have been defined.[1]
- Type 1. Multiple use. The colors of individual spots change color "both ways", for example: from blue to pink and vice versa. Note that if the 60% relative humidity spot changes color, then such HIC cannot be used again, as the 10% relative humidity and 5% relative humidity spots may have incorrect readings.
- Type 2. One-time use. The color of the indicator spots do not "change back"
Packing
J-STD-033 specifies rules related to packaging of components depending on the MSL level. For example, for MSL=3 components, one should:
- Bake the components before packing.
- Add a moisture indicator card (HIC).
- Add a moisture absorber (hygroscopic bag containing silica gel).
- Pack in a special sealed MBB (Moisture Barrier Bag).
- Place a label on the MBB bag with the MSID symbol and a description of the storage and baking requirements, as well as the sealing date of the bag.
Storing
Components sealed in a MBB can be stored for 12 months from the date the MBB was sealed, which is indicated on the label. If the manufacturer has specified a different storage time (e.g., 24 months), it should put the appropriate information on the label[1].
If the MBB bag has been opened after the storage time has expired, but the HIC indicates that drying is still not required, then components can be used[1]. I recommend additional caution to ensure, that there will be no unexpected issues (like a degraded solderability).
Once the bag is opened
MSL=1 components do not require opening time control due to moisture.
MSL=6 components always require drying after opening and before use for assembly.
Other types of components (MSL=2..5a) have a specific time ("Floor Life Clock") stated on the label per MSL level. Use the components within the specified time. Opening the bag causes moisture ingress, so we can imagine that a "Floor Life Clock" is started, and after it expires, the components cannot be used without drying first. This time (clock) can be "stopped" or "reset". Resetting causes the floor life clock to count anew.
Stopping the "floor life clock" involves placing components in a chamber with low humidity, less than 10%RH.
Resetting the "floor life clock" involves drying according to J-STD-033 Table 4-1 or to the manufacturer's recommendations. It is worth to know that for some cases, simply placing the components in a low-moisture chamber "resets" the clock. Details of "resetting" and "stopping" the clock are specified in Table 4-3[1].
Baking (drying)
If the components will be outside of a sealed bag or outside of a low humidity chamber for longer than the specified time (the floor life clock has expired), they should be baked according to Table 4-1. I recommend checking the component manufacturer's recommendations in this regard, as there can sometimes be significant differences.
Depending on the thickness of the component package and its MSL level, the baking time is determined for three temperatures: 125°C, 90°C and 40°C.
It is worth remembering that many components have leads coated with tin (Sn), and the baking process slightly reduces the solderability of the leads. Elevated temperature increases the intermetallic phases on the leads, so repeated baking can have a negative effect on solderability.
When baking, be careful with the trays. They sometimes become deformed and can give off impurities.
Use a dedicated oven for drying. This approach eliminates the risk of contamination of the components with various compounds from residues of other processes (curing varnishes, drying adhesives) that have been deposited in the oven.
Rework
Standard J-STD-033D recommends that when replacing a component on a circuit board, adjacent components should not be heated above 200°C. Some of them may be MSL>1 and may contain a significant amount of moisture. If such heating cannot be avoided, the PCB should be baked before. Rework should be performed in accordance with IPC-7711 procedures.
Derating
The floor life of components removed from MBB depends on the relative humidity and air temperature in the shop floor. J-STD-033 requirements were developed for conditions not exceeding 30°C/60%RH. If the temperature exceeds 30°C or the humidity exceeds 60%RH, then the standard provides rules for "derating," i.e., adjusting MSL rules to actual plant conditions. Details are provided in Chapter 7 of the standard.
Summary
Excessive moisture has a negative effect on components, which is particularly important in the reflow soldering process. Moisture sensitivity of SMD is classified as MSL levels and defined in J-STD-020, while the J-STD-033 standard establishes rules for handling moisture-sensitive components (packing, storage, use, baking).
Supervising moisture-sensitive components requires a number of activities. In terms of equipment, it is necessary to take care of an oven for baking components, a dry chamber with a humidity level of less than 5%RH for storing components outside of MBB bags. A very important aspect is the use of a good IT system for MSL tracking, which will be helpful in maintaining records (evidence) of meeting customer requirements.
It is also worth remembering that moisture in PCBs is a major challenge in the electronics industry.
It is necessary to provide adequate training for employees in the areas of receiving inspection, warehousing and production.
Footnotes
- IPC/JEDEC J-STD-033
- IPC/JEDEC J-STD-020